Evaluation of fracture surfaces with regard to damage development of cyclically loaded specimens made of C22E and 20MnCrS5
Within the framework of the planned research project, the aim is to identify the specifics of the fracture surfaces and to record the individual areas quantitatively in order to enable conclusions to be drawn about the material-mechanical processes and to assign them to the different fatigue stages.
In addition to the recording of fracture surfaces, the Olympus DSX 1000 also provides the possibility to quantify microstructures and phases as well as metallic and non-metallic inclusions, which is also an essential point for comprehensive material characterisation.
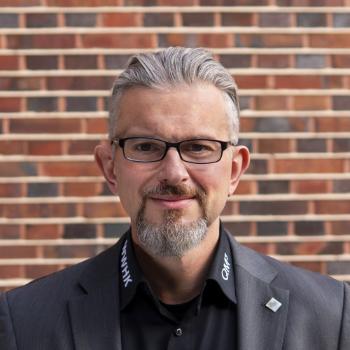
Vizepräsident für Forschung und Transfer, Studiengangsleitung: "Maschinenbau, Bachelor" "Mechatronik, Bachelor", Fachbereichsrat AING
- +49 631 3724-2389peter.starke(at)hs-kl(dot)de
- Campus Kaiserslautern
- Room H1-2010.1
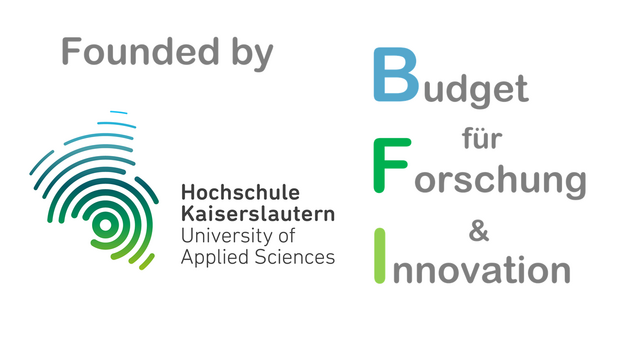
As part of the planned research project, fatigue specimens of the steels C22R and 20MnCrS5 will be subjected to conastant amplitude loading with different stress and total strain amplitudes. Within the framework of conventional fatigue tests, it is first of all not possible to make reliable statements with regard to macrocrack formation and propagation (only via the stress or total strain amplitude drop, although this is rather inaccurate). However, through the use of resistive and magnetics-based measurement techniques, which have been developed in recent years by the applicant and others, it is possible to at least record the onset of various material mechanical processes. It is therefore planned to carry out the fatigue tests up to various stages of fatigue and to break up the specimens rapidly in each case under nitrogen. Due to the strong cooling of the specimens and the high deformation speed, embrittlement occurs in the intended materials and further plastic deformation can be prevented as far as possible. The intended materials are body-centred cubic (bcc) lattice structures which, at high deformation rates and very low temperatures, change from the sliding fracture to the separating fracture systems with regard to their failure mechanism. This results in only a small amount of further deformation during the fracturing of non-cracked parts, which can be used to prepare the respective structural status. The fracture surfaces exposed in this way are examined under a light microscope and characterised fractographically. The results will then be used in two ways. Firstly, they will be correlated with the measured value curves of the electrical resistance and the magnetic Barkhausen noise. Thus, after completion of the planned investigations, it should be possible to assign discontinuities in the measured value curves selectively to the crack progress. Furthermore, this information is to be used as input variables in the simulation software PROST (PRObabilistic STructure calculation), whereby the crack propagation is to be made usable in an "inverse approach" for the prediction of the crack behaviour.
If this can be implemented, it will also be possible in future to provide information on the crack propagation behaviour in conventional fatigue tests for component design.