Research Area: Lightweight Design
The increasing scarcity and increase in the cost of natural resources is increasing the pressure to develop weight-optimized components in all areas and making the development of resource-efficient means of transportation indispensable. Lightweight construction plays a central role in moving systems, but especially in vehicle construction and the aerospace industry, since vehicle masses have a decisive influence on fuel consumption, both in current and future drive concepts. To achieve this goal, the development of customized high-performance materials can make a significant contribution. Furthermore, the lightweight construction potential can be exploited in an optimal way by using lastfallgerecht selected materials.
The activities in lightweight construction can be subdivided into metallic and non-metallic, polymer-based orientations. Another dimension of the project is explored through physically based structure optimization strategies.
Through the use of fiber-reinforced plastics (mainly glass, carbon and natural fibers) a significant reduction of the structural weight compared to comparable metal components can be achieved. As a matrix both thermosets and thermoplastics can be used. The focus of developments is also the combination of different materials (multi-material construction), the development engineer with new challenges in the development of novel textile structures in terms of design, construction, manufacturing process, bonding techniques and physical properties such. faced with thermal conductivity. A very good example of this is the door cladding of the Mercedes CLS class based on a natural fiber composite (see below).
Contact HTS "Lightweight Design"
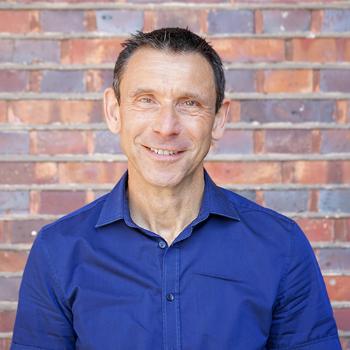
Studiengangsleitung: "Product Refinement, Master" "Refinement of Polymer and Composite Products, Master", Auslandsbeauftragter FB ALP, Fachbereichsrat ALP, Prüfungsausschuss ALP A FB ALP, Senatsausschuss für Internationalisierung
- +49 631 3724-7049jens.schuster(at)hs-kl(dot)de
- Campus Pirmasens
- Room B117